Beyond fossil fuels: Carbon-based chemicals without the emissions
- Chloe Coates
- Feb 7, 2024
- 12 min read
Carbon-based chemicals are critical to modern life—from the plastic packaging that wraps our food in the supermarket (polyethylene), polyurethane foams that insulate our homes, the nylon in our clothes, to the surfactants that we use to clean.
These chemicals, plastics and other carbon-based materials are commonly referred to as petrochemicals. To date, fossil fuels have provided abundant and inexpensive carbon feedstocks for these. As of 2018, petrochemicals were responsible for 14% of the total primary demand for oil and 8% of the demand for natural gas. And with this scale comes an emissions problem.
Petrochemical production is energy- and emissions-intensive throughout the lifecycle, and the rapid demand growth shows no sign of slowing down. Plastics alone were responsible for nearly 1.8 GtCO2e of emissions in 2015, and demand continues to rise, with the value of the petrochemical industry rising at a rate of nearly 8% per year since 2010.
Just six molecules constitute the main building blocks of the carbon-based petrochemicals and their production. These six upstream chemicals are:
methanol (CH3OH)
ethene (C2H4) and propene (C3H6) (also known as olefins / alkenes)
benzene (C6H6), toluene and xylene (also known as aromatics / BTX).
The global mass flows of petrochemicals are displayed in the Sankey diagram below (the original paper is excellent and highly recommended reading). Whilst the absolute volumes are larger today, it shows the critical role played by a small number of upstream chemicals, which are precursors for an enormous number of chemicals and materials used in a wide variety of our modern-day products.
The ammonia (NH3) used for fertilisers is considered a petrochemical as its production relies heavily on fossil fuels—steam methane reforming is used to produce the hydrogen needed to make ammonia. However, as discussed in our previous article on decarbonising ammonia, renewable hydrogen from electrolysis and emerging electrochemical pathways provide routes to low-carbon ammonia production. And crucially, ammonia is not a carbon-based chemical, the nitrogen in the ammonia can be sourced from the air.
But renewable hydrogen alone is not enough to decarbonise carbon-based chemicals. We also need renewable sources of carbon to replace oil, gas and coal in supplying the carbon-based chemicals society depends on. This is the focus of this blogpost.
Where do the emissions come from?
Fossil fuel extraction
The extraction of fossil fuel feedstocks results in fugitive methane emissions, which is significant problem due to methane's high global warming potential relative to CO2 (GWP100 = 28 CO2e). These fugitive emissions were responsible for 5.8% of GHG emissions in 2020, or approximately 2.9 GtCO2e, so given that petrochemicals account for ~10% of fossil demand this results in emissions of approximately 0.3 GtCO2e from fugitive emissions alone. If we consider the near-term warming effect of methane, with its GWP25 = 84 CO2e, then the problem looks even worse—just the extraction of the fossil fuels for petrochemical production results in 0.9 GtCO2e per year.
Upstream production
The production of these upstream chemicals from oil, gas and coal involves processes that require high temperature heat (>800°C)—obtained from the burning of fossil fuels. Their production proceeds either via steam reforming of methane, or gasification of coal, to produce syngas (CO + H2), which acts as the precursor to methanol and the hydrogen source for ammonia. Ethene and propene are obtained from high-temperature catalytic cracking of oil fractions, which generates 1.5 tCO2e per tonne of ethene produced, resulting in >260 MtCO2e/year for that process alone. Most of the supply of BTX aromatics and C4 chemicals (those with four-carbons in the molecular backbone) is sourced from refineries as a by-product of fuel production. Olefins can also be produced from methanol (methanol-to-olefins, or MTO), whilst the production of BTX chemicals from methanol is under development, but is currently extremely expensive.
End-of-life
Determining the end-of-life emissions for petrochemicals is non-trivial; in some cases, such as for long-lasting PVC pipes (polyvinylchloride), the carbon is essentially sequestered for decades, whereas for single-use plastics and surfactants the embodied carbon is often released. Attempts to reduce these downstream emissions include reducing usage either by reducing demand or achieving material efficiency improvements. In terms of emissions, the worst end-of-life pathway for plastics is incineration—currently 10% of plastics are incinerated. Landfill could in theory ‘sequester’ carbon in plastics but might also release methane via bacterial decomposition. Recycling also provides alternative feedstock for plastics/other petrochemicals and thus minimises extraction and production emissions.
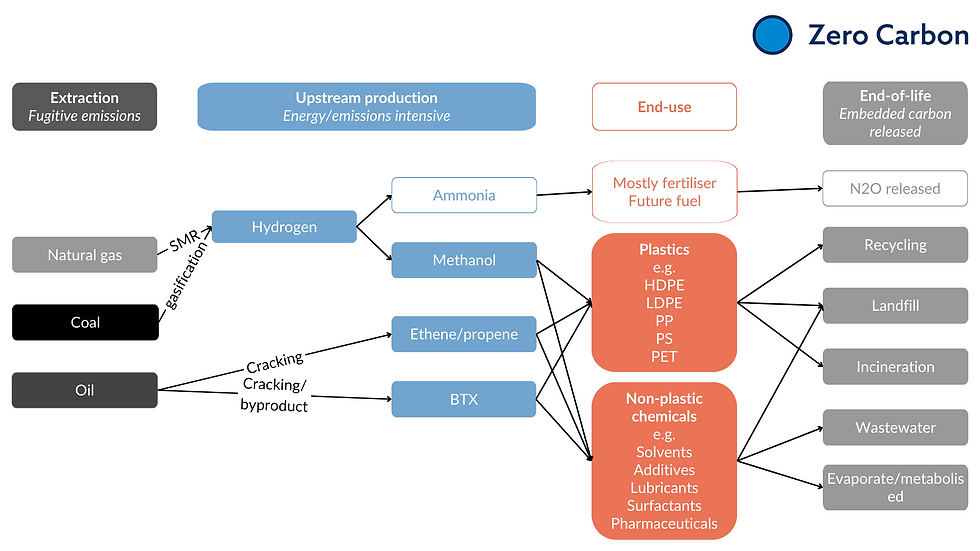
What are the biggest levers for decarbonisation and where will we get our carbon from?
Plastics and chemicals aren’t going anywhere. Given the unique physical and chemical properties of hydrocarbons, it is unlikely that we can replace them with carbon-free, lower emissions alternatives. Analysis has shown that substituting plastic products with alternatives—such as paper, wood or aluminium, is rarely an improvement in terms of emissions. (There are of course, other environmental and ecological benefits to reducing plastic consumption and waste mismanagement.) And reducing plastic packaging on food, for example, could displace emissions elsewhere, in the form of increased spoilage and therefore more agriculture-related emissions. So how do we benefit from the myriad applications of plastics and chemicals, but reduce the emissions-intensity?
There are two main levers for decarbonising chemicals: feedstock substitution and process electrification/decarbonisation, and for full decarbonisation they must be deployed in tandem.
Process electrification / decarbonisation
For conventional petrochemical production, not only are the feedstocks fossil-derived, but the processes are extremely energy intensive–and this energy is generated by fossil fuels. Significant emissions reduction could be achieved by using renewable-powered electrified processes, or less carbon-intensive alternatives. These include electric crackers, membrane-based separation technologies and carbon capture and storage. Electric crackers are under development that—if run using renewable electricity—would cut emissions from cracking by 90%. Membrane-based separation technologies are being developed as an alternative to the energy-intensive fractional distillation columns (e.g. UniSieve, Via Separations). But this still leaves the problem of fossil feedstocks.
Alternative feedstocks
We need to find a source of carbon to replace our fossil feedstocks, and there are many–in biomass from plants, from the CO2 in the air, to human waste and discarded plastics. None is a perfect solution, and none is currently price-competitive with fossil fuels without a carbon tax, but each has advantages and challenges depending on feedstock availability and clean energy availability. Either way, we will probably need some or all of them. Here we review the alternative feedstocks, and the technologies we need to develop to exploit them.
There are at least as many conversion technologies as there are different feedstocks–both existing and emerging technologies. These include (i) electrified thermochemical processes, (ii) electrochemical processes that use electricity to drive reactions rather than heat (electrolytic or plasma-based), or (iii) biochemical approaches, for example using microbes or enzymes, that can catalyse energy-hungry reactions under ambient conditions.
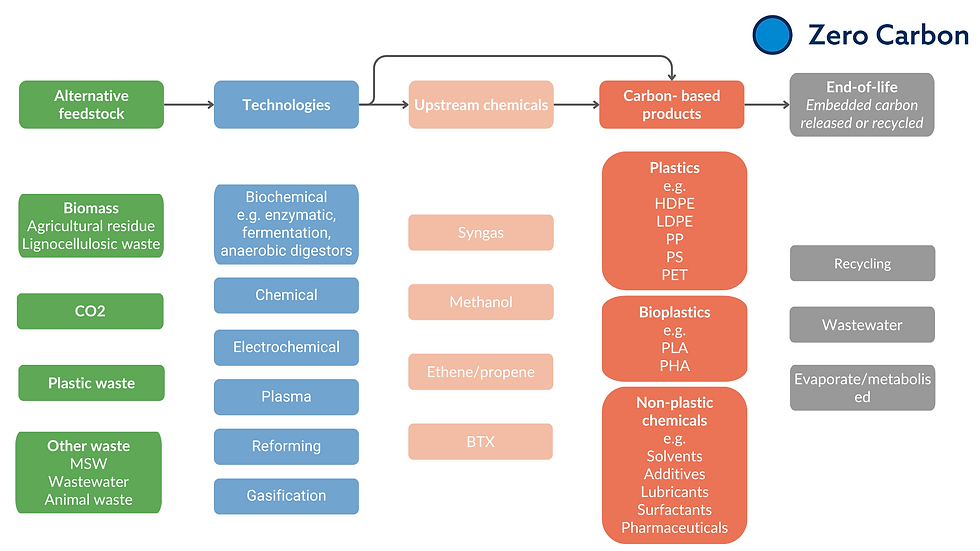
Biomass
Biomass has long been touted as a replacement for petrochemicals, and is already used on a small scale. Just as with fossil-based refineries, the use of biomass as a fuel for bioenergy has been the main product of biorefineries to date. But given the availability of low cost wind and solar, and the electrification of transport, it is clear that it will be higher impact to preserve these bio-sourced carbon atoms for petrochemicals, rather than energy.
Biomass-derived chemicals have the potential to be carbon negative (or carbon neutral depending on the product and its end-of-life emissions), but this is dependent on emissions associated with processing and transport of the biomass. There is also the question of land-use: the ethical question of whether crops-for-chemicals displace food crops, whether increased demand would lead to increased land-use change (which is emissions intensive and damages ecosystems and natural carbon sinks), as well as the N2O emissions and water stresses associated with agricultural practices generally.
The use of agricultural residues avoids many of these issues, but certain structural challenges remain: the distributed, often seasonal supply of feedstocks and challenges with storage to avoid decomposition. These ‘waste’ feedstocks may also become commodities in themselves as demand (for platform chemicals, or for energy use) increases. Startups in this space relying on waste feedstocks could face increasing competition for access to them, potentially leading to increased costs. Biomass feedstocks are particularly well-suited to bio-processing: exploiting enzymes or microorganisms to provide low-energy and specific routes to more downstream chemicals directly (e.g. ZCC portfolio company twig's sustainable ingredients). Bioplastics are another obvious example of substituting fossil-derived monomers for biological alternatives, although these don't always have the same properties.
How much biomass would we need to supply all our carbon-based chemicals? And how much land would this require? We can make a rough estimate:
Demand for petrochemicals (excluding ammonia) is currently around 500 Mt
If biomass to product conversion is around 50% then we would need 1 Gt of biomass–this is more than the world’s annual wheat consumption (around 800 Mt)
Given agricultural productivity of ~10 t/hectare (the approximate yield of American maize–the global average is typically lower) this would be a land requirement of 100 million hectares (or 1 million square km)
This would represent just under 10% of current agricultural land used to grow crops (11 m square km), but under 3% of the land use for livestock grazing and feed (37 m square km).
This land area is roughly equivalent to four times the area of the UK. Whilst 10% of current cropland seems like a large number, in a future where land-use livestock is drastically reduced, it could make sense to convert cropland for animal feed to cropland for petrochemicals. Either way, we will probably need other feedstocks too.
We also need to maximise our use of agricultural waste, including lignocellulosic biomass. Lignocellulosic biomass, also known as woody biomass, is typically obtained from agriculture and forestry waste. It consists of three chemical components: cellulose and hemicellulose, and an aromatic-rich polymer called lignin. Lignocellulose is a feedstock for the pulp and paper industry, where the cellulose is separated to be used for paper. The lignin component (typically ~30% of lignocellulosic residues) offers the largest natural source of aromatic motifs for BTX chemicals. But these residues are challenging to process into chemicals, so are usually just burned for heat. Fast pyrolysis can convert biomass into bio-oil containing oxygenated hydrocarbons amenable as feedstocks for aromatics production. Gasification also yields syngas as a platform chemical for subsequent transformation. Aromatics directly from lignin byproducts could be enabled by low cost separation of recalcitrant lignocellulose streams and conversion of the complex lignin compounds. ZCC portfolio company Level Nine are doing just this, using engineered biocatalysts to lower the cost of converting lignin to BTX (as well as e.g. Bloom Biorenewables).
Carbon dioxide
We can also use carbon dioxide as our carbon source for chemicals, often referred to as carbon capture and utilisation (CCU), carbon valorisation or CO2-to-X. It is already chemically feasible to make many of the chemicals and fuels we use from CO2, using hydrogen (from renewables-driven electrolysis) as a co-reactant. The “reverse water-gas shift” between CO2 and hydrogen is a thermochemical (heat-driven) reaction that produces syngas (CO + H2) as a platform chemical which can then undergo numerous well-studied reactions (Fischer-Tropsch, Sabatier) to produce synthetic fuels or methane, amongst many other possibilities.
There are two main challenges. Firstly, these reactions are currently extremely expensive, and depend on the cost of clean hydrogen and the cost of captured CO2, both of which are not yet produced at scale. This challenge derives from the stability of carbon dioxide, it’s simply quite chemically unreactive, and so a lot of energy is required to get it to react—this energy comes from hydrogen, which is energy intensive to produce electrochemically. Many new technologies are currently being developed to convert CO2 to chemicals using new electrochemical (e.g. Dioxycle, Twelve, CERT Systems), plasma (e.g D-CRBN) or biochemical approaches (e.g. LanzaTech).
We need to design and scale cheap direct air capture technologies. There is an impact risk with scaling CO2-to-X: in order to be truly carbon neutral using CO2 as a feedstock requires CO2 from direct air capture, or ocean CDR. Although likely to scale sooner, using point-source-captured CO2 at best represents an efficiency improvement of doing more with emissions, but the emissions to do not go to zero.
Waste plastic
Waste plastic can be used as a hydrocarbon feedstock. Whilst mechanical recycling is the most energy efficient way to reuse waste plastic, only HDPE and PET are widely recycled in this way, and suffer from degradation in the process, so cannot be infinitely recycled.
Plastics such as polyethylene, polypropylene and polystyrene (about 50% of annual plastic waste) most closely resemble the composition of fossil fuels; they contain only carbon and hydrogen, meaning they have higher carbon and energy contents than other plastics, and indeed other carbon feedstocks such as biomass or other waste streams.
From an emissions reduction perspective, using current plastics that were originally from fossil fuels, does not have the same potential to be carbon negative as for biomass or DAC-CO2, but recycled plastic feedstocks will play an important role as we move towards a closed loop system. In future, the inputs of this system will come from various carbon sources, when we have moved away from fossil fuel feedstocks entirely. When we aren’t digging carbon out of the ground via fossil fuels, we will need an efficient system of recycling carbon to make all the chemicals and products we need. It is critical that new technologies are developed to recycle the more challenging feedstocks including mixed or contaminated plastics.
There are a multitude of different technologies, either existing or under development, to exploit plastic waste, from biochemical approaches using enzymes to depolymerise plastics to their monomers (e.g. ZCC portfolio company Epoch Biodesign), chemical recycling approaches (e.g. DePoly), as well advanced gasification and pyrolysis approaches, including using plasma (e.g. Cyclize) to generate syngas or oil-like feedstock. These conversion technologies that break down the plastics into small building blocks are more energy intensive than mechanical or depolymerisation technologies, but by producing platform chemicals like syngas can act as a fossil-free feedstock to a huge range of chemicals (and fuels). They could be particularly useful for hard-to-recycle mixed plastics, where separation of chemistries and monomers is a challenge.
Municipal solid waste, wastewater sludge, animal waste
Municipal solid waste (MSW) offers another potential waste feedstock for petrochemicals production. Though more heterogeneous, MSW streams contain carbon-rich materials like paper, food waste, textiles and non-recycled plastics. Techniques like pyrolysis and gasification can upgrade carbon in MSW into basic chemicals. But extensive sorting and separation is first required to remove incompatible materials and minimise undesirable contaminants in the final output streams.
Biogas can act as a source of low cost biogenic CO2. Biogas is already collected in many municipal solid waste (MSW) facilities via landfill gas recovery systems, typically as mixtures of methane (CH4) and carbon dioxide (CO2). It is also produced from wastewater and animal waste using anaerobic digesters. Most biogas is either used directly as a low grade fuel or upgraded to enhance the CH4:CO2 ratio, to provide higher quality biomethane for fuel. An emerging alternative is the use of microbial electrolysis to produce hydrogen with CO2 as a side product, giving a CO2-free fuel (the hydrogen) and biogenic CO2 for chemical synthesis. Optimising input streams can also lead to improved yields (e.g. Methaplanet).
What chemicals do we target & what technologies do we need?
The challenge lies in the tension between impact and margins. In order to achieve the biggest impact on decarbonisation, we should target production of the upstream, emissions-intensive precursor chemicals, including methanol, alkenes and BTX aromatics. But these are also the low-value, low-margin commodity chemicals, where there is little scope for end users to pay a green premium.
High-value specialty chemicals can be the first products for startups go-to-market strategy. Early market entrants that are using non-fossil feedstocks tend to be high value specialty chemicals; these can bear the higher costs of renewable feedstock conversion, while avoiding competition with more established technologies for limited supplies of renewables-based hydrogen and energy. These companies target specialty products like polycarbonates, polyols, and battery precursor diethyl carbonates to maximise profit margins in return for higher prices.
But we need to decarbonise the low and medium-margin chemicals too. Syngas can be produced from almost any feedstock, and can be—or is already—a precursor for most chemicals. The ability to act as a drop-in solution for customers seeking fossil-free alternatives makes it an attractive prospect in the short term and will be increasingly competitive as the cost of green hydrogen is reduced.
So how will we decarbonise chemicals?
Scientist entrepreneurs: Firstly, we need visionary entrepreneurs to design, develop and scale technologies that utilise fossil-free feedstocks, and can use renewable electricity as the energy input. If this is you – please get in touch!
Scale supply chains: In order to fulfil the demand for decarbonised chemicals we will need to scale the fossil-free supply chains, including for low-carbon hydrogen, CO2 and waste biomass, as well as for renewable energy deployment. Current petrochemicals refineries benefit from huge economies of scale, with highly integrated production of upstream and downstream chemicals, where waste heat from the production of upstream chemicals is used later, for reactions that require milder conditions.
Regulation: There is increasing regulatory pressure to move towards more circular and sustainable feedstocks. For example, in 2023 the Environment Committee of the European Union adopted their position on a proposal to mandate minimum amounts of recycled material and encourage collection and separation of different types of packaging.
Consumer pull: Consumer demand is also driving commitments from corporates: more than 80 global CPG, packaging, and retail companies have made public commitments to reach recycled content in their packaging by 15-50% by 2025.
Policy: Policy incentives will be critical to funding the first stages of development of these supply chains, including, for example in the US, as part of the IRA, companies can claim the 45V Hydrogen Production Tax Credit, which awards up to $3 per kg of hydrogen produced to projects with a lifecycle GHG emissions intensity < 0.45 kg CO2e/kg H2.
References and further reading
Mapping Global Flows of Chemicals: From Fossil Fuel Feedstocks to Chemical Products P. G. Levi and J. M. Cullen Environ. Sci. Technol. 52, 4, 1725–1734 (2018)
Bioplastics for circular economy J.-G. Rosenboom, R. Langer and G. Traverso, Nature Rev. Mater. 7 117-137 (2022)
Don’t bury money: how to create value from CO2 Iris ten Have, Extantia (2022)
Decarbonizing Chemicals Part One: Sectorwide Challenges Will Intensify Beyond 2030 S&P Global (2023)
Can Carbon Help Decarbonize Chemicals? BCG Deep Tech article (2023)
Net-zero emissions chemical industry in a world of limited resources Paolo Gabrielli et al. One Earth 6, 682-704 (2023)
Comments